DIY vs Buckeye ‘Cradle to Grave’: What’s the Best Approach to Terminal Hardware Lifecycle Management?
DIY vs Buckeye ‘Cradle to Grave’:
What’s the Best Approach to Hardware Lifecycle Management?
Mobile computers and other specialized hardware have delivered powerful new capabilities that improve speed, efficiency, and productivity in rail and port terminals. But realizing the value of your hardware investment isn’t as simple as buying tablet devices and placing them in the hands of field operations teams.
Devices require constant management and maintenance to keep them in proper working order. Terminals require durable hardware that can withstand the wear and tear of a rugged work environment—and even then, those facilities need a plan to repair and replace damaged assets. And personal devices must be constantly managed and monitored to make sure they’re used in alignment with company policy.
All of these ongoing tasks fall under the umbrella of hardware lifecycle management—a strategic framework for maximizing the ROI of your terminal’s technology investments. Effective hardware lifecycle management improves the longevity, availability, and performance of your terminal hardware, which in turn delivers tangible performance gains for your field operations teams.
Terminals have two options for implementing hardware lifecycle management:
- DIY: Your in-house technical teams handle everything on your own: hardware deployments, device management, software updates, repairs, and everything in between.
- Working with a lifecycle management partner: At Buckeye Mountain, for example, our cradle-to-grave approach encompasses the full lifecycle for every hardware solution. From creation to disposal, we manage the full lifecycle thoughtfully and responsibly, ensuring it aligns with your operational and environmental goals.
Let’s dive into the pros and cons of each approach—and lay out the business case for partnering with Buckeye Mountain.
What it Means to Tackle Lifecycle Management with a DIY Approach
Businesses that handle hardware lifecycle management in-house must pull from their existing personnel and resources to enable this strategic framework.
Inadequate resource support can undercut the effectiveness of DIY lifecycle management. This lays the groundwork for a number of issues which can impact the cost and value of these hardware investments:
Higher Rates of Hardware Downtime
One of the core objectives of lifecycle management is to maximize the availability of hardware for your field ops teams.
Equipment breakdowns, malfunctions, and device damage are inevitable in challenging rail and port environments. Any instance of hardware downtime can impede operations and overall business performance.
“Speed is critical because it equates to minimal downtime—especially when dealing with rail and port terminals. In a rail yard, even 10 minutes of downtime can feel like a significant stoppage for workers on the ground and can have costly effects on a terminal.”
Erica Toney, Southeast Operations Manager at Buckeye Mountain
An Increase in Worker Distractions
In a DIY scenario, hardware distractions can come in two forms.
The first is the amount of time workers end up spending to manage hardware and software on their own instead of fulfilling their primary work responsibilities. These management tasks cancel out some of the productivity gains of the hardware—while also increasing the risk of human error in hardware management.
In some cases, workers may use these devices to access applications or other content that is prohibited on the job site.
“In a rail yard, you can’t have a train and engine employee—someone responsible for counting and assessing train cars—standing there watching YouTube on an iPad,” says Toney.
But without access to industry-leading mobile device management systems and other remote device management capabilities, DIY lifecycle managers may not have the tools they need to enforce these device policies.
Excessive Repair and Maintenance Costs
Without a readily available, scalable process for handling hardware maintenance and repairs, the DIY approach is likely to result in high repair and maintenance costs that impact your organization’s capital budgets.
If organizations don’t anticipate these costs and allocate an appropriate budget, DIY lifecycle managers could face situations where their capital budget is exhausted before the year’s end, resulting in longer delays for device repairs and even higher rates of equipment downtime.
Even with a budget in place, the lack of proven, efficient repair and maintenance processes is almost certain to inflate the cost of performing these services in-house.
What Terminal Workers can Accomplish When They Aren’t Tasked with DIY Lifecycle Management

In-house lifecycle management may seem more affordable because it doesn’t create a new line item expense. But the apparent up-front savings of a DIY approach only ends up stealing resources and productivity away from other parts of your operations, forcing terminal workers to set aside other responsibilities that are essential to yard operations.
By lifting the burden of a DIY strategy, those workers can then prioritize their core requirements and contribute to other key terminal initiatives, including the following:
Uninterrupted service during natural events
A severe storm or other natural event can threaten a terminal’s ability to maintain operations. When lifecycle management is being handled in-house, terminal workers may need to focus on getting devices and systems back online to mitigate downtime and keep operations running.
But with a partner like Buckeye Mountain managing this hardware, terminal workers can instead focus on performing their regular tasks. Buckeye can manage everything remotely, and terminal operations can proceed uninterrupted.
“We work closely with our customers—not just on the hardware side, but also to ensure failovers are in place for situations beyond their control,” says Toney. “We understand that outside of the day-to-day hardware support involved in lifecycle management, there are mission-critical scenarios where operational continuity is non-negotiable.”
Ensuring Compliance with Rail Operations Regulations
As terminals move from paper to electronic documentation, materials like rule books and safety documents must always be accessible. This access needs continual oversight to ensure that a failed app update or other technical issue doesn’t restrict access to essential materials.
DIY lifecycle management often leans on terminal workers to make sure this documentation is available—instead of using that documentation to support terminal safety and other compliance requirements.
With a partner like Buckeye managing devices remotely and ensuring continual access, terminal workers can spend more of their time using that documentation to enable more efficient, compliant operations.
The Benefits of Outsourced Lifecycle Management: What Buckeye Mountain Brings to the Table
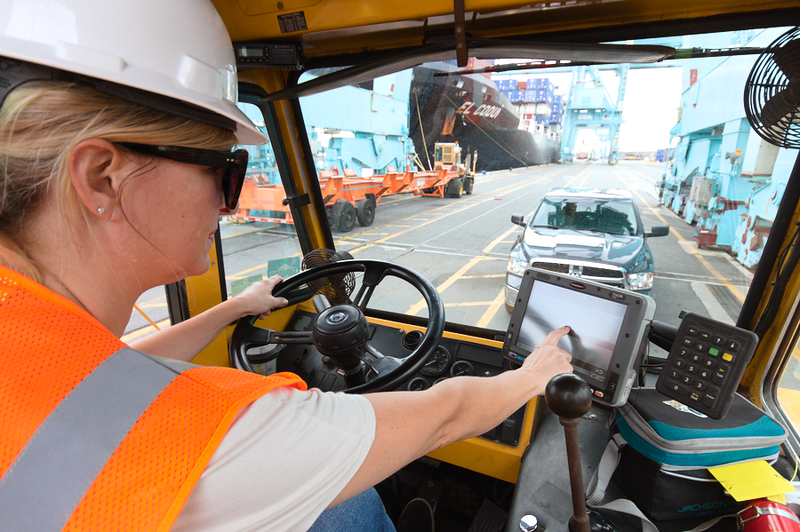
Terminal hardware is a significant investment. A lifecycle management partner like Buckeye Mountain can help you maximize the ROI of that investment, equipping your organization with operational efficiencies, hardware expertise, and agile support that would be infeasible and unsustainable to allocate internally.
Here’s what you can expect from Buckeye Mountain’s cradle-to-grave lifecycle IT services:
Exceptional Customer Service and an Agile Approach
Hardware lifecycle management is a big part of what we do. Whether you’re faced with managing inventory, configuring devices, coordinating repairs or deploying new devices, Buckeye can do it faster and more efficiently than your in-house personnel—even when your needs arise outside of traditional working hours.
“Our commitment to exceptional customer service is evident in both our business-hour service centers and our 24/7 support operation center, which all thrive on Buckeye’s customer-first culture,” says Toney. “This approach exemplifies how we efficiently manage the speed and demands of hardware lifecycle management.”
As terminal technology and hardware infrastructure evolve, Buckeye Mountain also retains the agility to help address emerging changes and seize opportunities to procure new hardware that best serves your facility’s long-term goals.
“Our customers are understandably focused on their day-to-day operations—which means they aren’t always paying attention to the long-term trajectory of their technology, including whether devices are outdated or approaching the end of their lifespan,” says Toney. “Part of our ‘cradle-to-grave’ approach involves keeping track of devices and operating systems nearing the end of their life cycles while understanding the future of projects so we are able to set our customers up for seamless transitions into new hardware rollouts.”
Erica Toney, Southeast Operations Manager at Buckeye Mountain
Timely Device Management and Repair
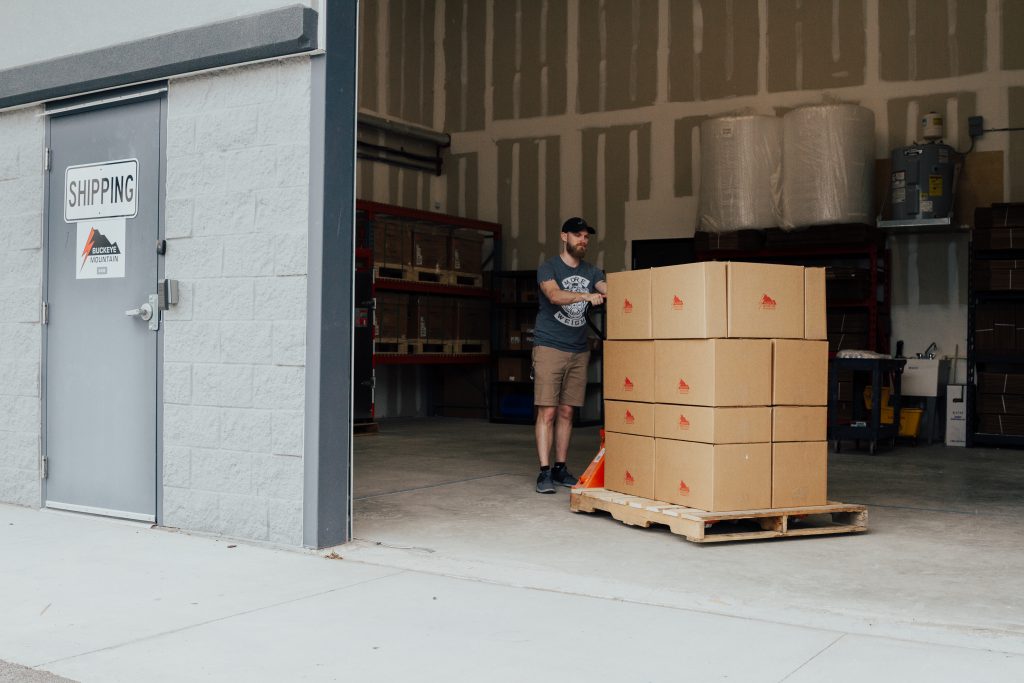
Buckeye Mountain takes on all responsibility for device management and repair. Our scalable device service allows for fast, cost-effective repairs that spare our customers the headache of worrying over unexpected hardware costs. We execute repairs quickly to minimize device downtime and keep terminal operations rolling.
“For us, this means offering same-day shipments for devices when needed, immediate remote support for resolvable issues, and being consistently accessible during operational hours,” says Toney. “This approach exemplifies how we efficiently manage the speed and demands of hardware lifecycle management.”
An Unmatched Partner, from Procurement to Replacement
Our lifecycle management services are comprehensive. We don’t leave any gaps for our customers to fill, and we pride ourselves on being a technology partner that adds value at every stage of the hardware lifecycle.
“A true partnership means both parties are equally invested in the success of the relationship,” says Toney. “At Buckeye Mountain, we’re deeply integrated into our customers’ experiences. We’re part of their successes and their challenges. We remain fully engaged throughout every phase of the lifecycle management process, ensuring we’re not just a vendor but a true partner in their technology journey.”
Erica Toney, Southeast Operations Manager at Buckeye Mountain
Manage hardware lifecycles at your own risk
Effective lifecycle management isn’t something you can piecemeal from your existing internal resources. It requires expert oversight, long-term strategic planning, and the freedom to quickly take action at scale without interfering with terminal operations.
A DIY approach puts your hardware ROI at risk—and could lead to a plague of inefficiencies and disruptions spilling over into your terminal operations. Buckeye Mountain can help you avoid this outcome while enabling the efficiencies, productivity gains, and long-term cost controls you envisioned when investing into upgraded terminal hardware.
Put your trust in Buckeye Mountain’s lifecycle management expertise.