Before You Buy: Considerations for Upgrading and Replacing Terminal Hardware
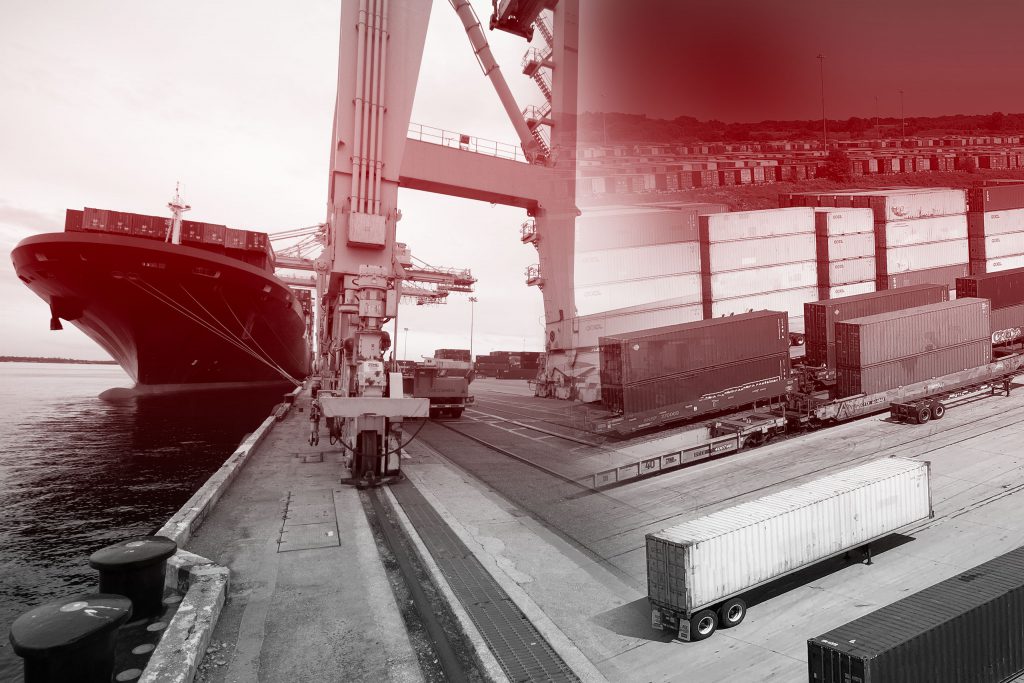
BEFORE YOU BUY: Considerations for Upgrading and Replacing Terminal Hardware
Equipment breakdowns are part of daily life on marine and rail terminals, as is purchasing and installing new terminal hardware to replace outdated and defunct equipment. Procurement managers purchasing equipment are often faced with an all-too-common scenario: take all equipment training, maintenance, and repairs in-house or feel locked into a vendor-specific support agreement when purchasing that equipment.
It’s only later—often a few months after declining offers of additional ongoing vendor support—that they return to the vendor in search of faster, cheaper, and more consistent support than what their in-house professionals or hardware-specific vendors can provide.
“When you add maintenance and repair to the workload of in-house technicians, you end up pulling resources away from core operations,” says David Fajardo, Manager of Field Technical Services at Buckeye Mountain. “Suddenly, there’s a man-hour cost to fixing hardware on top of the operational cost of equipment downtime—which turns every small problem into a five-alarm fire.”
The difficulty of maintaining equipment internally only increases over time. Terminal operating systems are becoming more intelligent and more complex—so is the new equipment deployed on the terminal. As a result, maintaining and repairing this equipment has become a heavier lift, increasing the strain placed on in-house technicians.
Buckeye Mountain’s field technical support services are designed to alleviate this burden, freeing up in-house technicians and resources to focus on supporting the terminal’s core operations. Terminal managers can coordinate planned, strategic equipment updates that prevent resource exhaustion and operational downtime by outsourcing equipment maintenance and repair to a trusted partner.
Read on to find out how our “boots on the ground” approach can help improve equipment availability and long-term value at your terminal while supporting better distribution, logistics, and other operational efficiencies for your customers.
Understanding the Strategy Behind Purchasing the Hardware
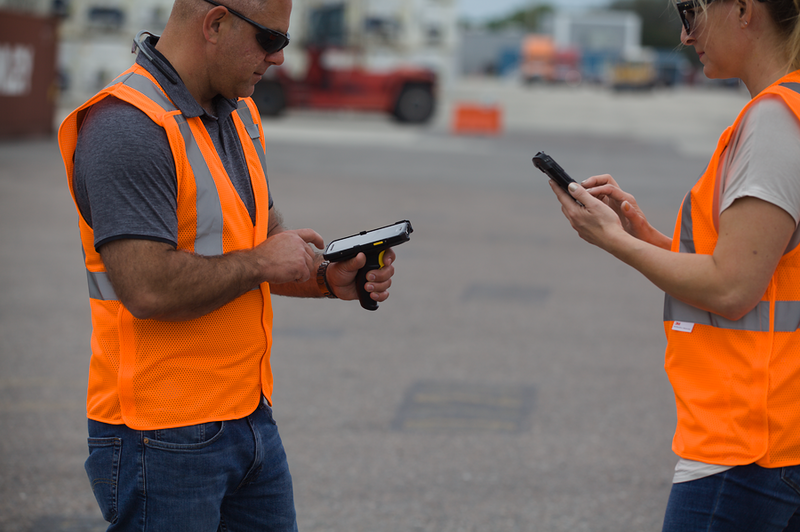
Purchasing the right hardware is only part of a successful procurement process. Before that purchase, procurement leaders face several strategic decisions that will affect the performance and value of that equipment throughout its lifespan.
By making these decisions ahead of your purchase, procurement managers can work with field operations leaders to determine the best approach for managing the equipment’s maintenance, repairs, asset management needs, and technical support.
Maintenance Plan and Warranty
Maintenance plans and equipment warranties help set the foundation for the long-term value you create from your hardware investment.
Warranties protect your company if your new equipment doesn’t meet quality assurance expectations. Meanwhile, a robust maintenance plan is critical to ensuring hardware receives preventative maintenance that reduces equipment failures and operational downtime.
“With almost any hardware installation we perform, we try to set up some sort of preventative maintenance plan,” says Fajardo. “You always want to correct issues before they become a problem.”
Before purchasing your hardware, find out if preventative maintenance is included in the purchase to maximize the longevity and reliability of your asset. Review your warranty carefully to understand the type of coverage you can expect if problems arise within the warranty period.
Asset Management
A comprehensive asset management strategy is critical to tracking hardware maintenance and servicing across the asset lifecycle. This is particularly important for terminals tracking many pieces of hardware facing unique maintenance needs and different stages of their lifecycles.
Whether your on-site field operations team or a third-party service provider handles your asset management, ensure you have a clear plan for managing new hardware purchases alongside your existing technology.
Regular hardware auditing should be a subset of your asset management strategy. Hardware auditing helps you track physical assets that you may reallocate within the terminal, and it supports preventative maintenance by making sure upcoming parts replacements and other asset management tasks are performed on schedule.
These audits are necessary to confirm that all equipment operating at your terminal is still meeting expectations regarding performance, efficiency, and any applicable compliance requirements.
Configuration and Repairs
Routine configuration of equipment ensures that your hardware is optimized for peak performance. Hardware relocated or utilized for a new purpose may need to be configured to its new environment and requirements.
Hardware configuration and repairs can disrupt your terminal’s work environment. Strategic planning is needed to coordinate repairs and servicing so that operations experience minimal disruption, if any.
Terminals tasking hardware configuration and repairs to in-house technicians may face a greater risk of disruption due to limited labor and resource flexibility: since in-house technicians are juggling hardware repairs alongside a laundry list of other responsibilities, they may not have the luxury of scheduling repairs during periods of non-peak workloads for the facility. Disrupted operations can increase material costs for your customers and the facility itself.
Tech Support and Downtime
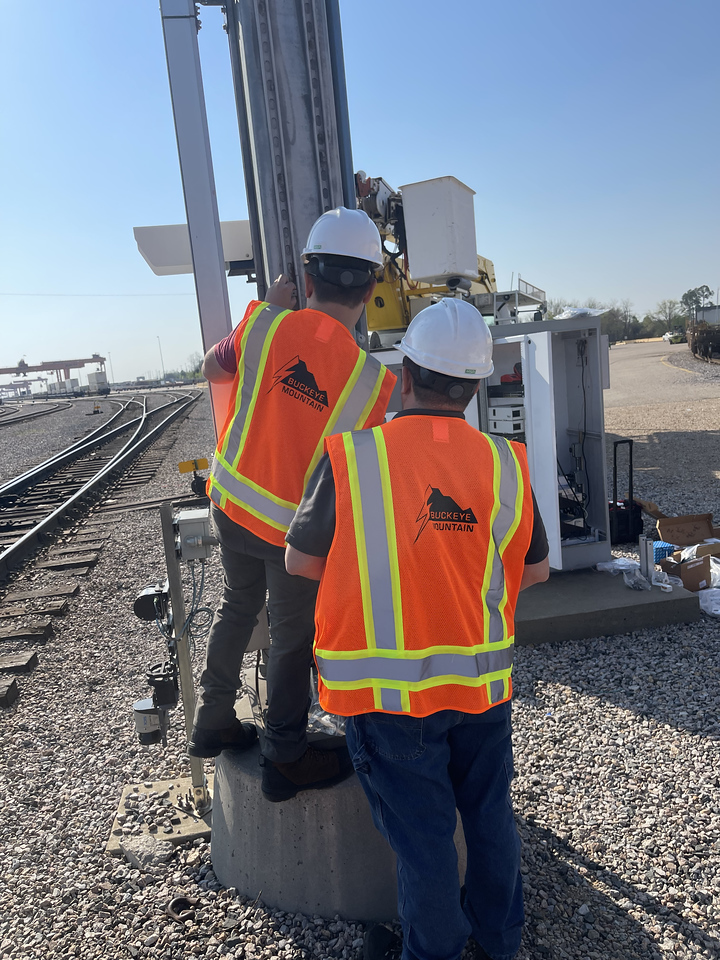
Equipment failures and other hardware issues can have a disastrous impact on terminal operations, resulting in significant outages that bring operations to a halt and cost the facility—and its customers—revenue.
When technical issues arise, a single in-house technician often needs more resources and bandwidth to quickly resolve the issue, leading to extended downtime and mounting financial losses. Professional support services, like Buckeye Mountain, on the other hand, are better equipped to respond with multiple technicians in the field who can quickly resolve the issue and bring your equipment back online.
“Technical issues can be a daily occurrence at some terminals, and many of these issues must be addressed manually by on-site technicians,” says Fajardo. “Since Buckeye knows how to install this hardware correctly, though, we’re able to reduce the frequency of these issues—and if something goes wrong, we’re right there to help.”
Accounting for Long-term Cost vs. Long-term Value
Equipment costs don’t end when you purchase your new hardware. But, the expense incurred over that equipment’s lifespan depends on your strategy for handling maintenance and repairs, minimizing equipment downtime, and maximizing the lifespan of your assets.
Higher costs don’t always result in less value for your investment. With equipment servicing, the opposite is often true: proactive spending for preventative maintenance and repair can substantially increase potential value creation from your equipment.
Procurement managers can help optimize costs and maximize long-term value potential by setting up an equipment servicing plan that prioritizes cost-efficient spending and long-term equipment health.
Increasing Longevity while reducing downtime
Equipment upgrades and replacements deliver an immediate impact to terminal operations. Even for procurement managers, it’s easy to get stuck on those short-term gains and overlook the long-term implications of that hardware investment.
In the end, though, the overall value each asset delivers for your organization will be determined by its longevity, long-term costs, and performance across the equipment lifecycle. Your equipment servicing plan directly affects each of these success metrics.
“It’s just like your car: If you take care of it, it’s going to last longer,” Fajardo says. “We’re like the mechanic working on your car: We keep the equipment well-maintained so that terminal operators get more longevity from each asset—and, in turn, get a better return on their hardware investment.”
According to Fajardo, this approach has enabled Buckeye Mountain to add years to the lifecycle of the customer equipment it manages. Thanks to Buckeye’s proactive maintenance, companies hoping to get five years of service out of a single asset regularly enjoy seven or eight years of service from that equipment.
The Impact of Repairs, Support, and Maintenance on Capital Budgets
Poor asset management practices can lead to inconsistent and delayed equipment maintenance, along with an increase in preventable repairs. These inefficiencies can result in budget overruns that leave your operations team with broken equipment and no room left in the budget for repairs.
In-house asset management can increase your organization’s exposure to these increased costs—especially if asset management is handled on a case-by-case basis when something needs repair. Since in-house technicians must juggle equipment maintenance and repair, among other tasks, costly delays are all but inevitable.
“We had one customer who moved away from our ‘boots-on-the-ground’ approach to bring asset management in-house and save on equipment servicing costs,” says Fajardo. “They quickly realized they lost a lot of asset management expertise that Buckeye Mountain brings to the table. We do things beyond scope to ensure our customers are taken care of—and we have an internal structure for managing assets that other companies can’t match.”
How Buckeye Mountain Adds Value
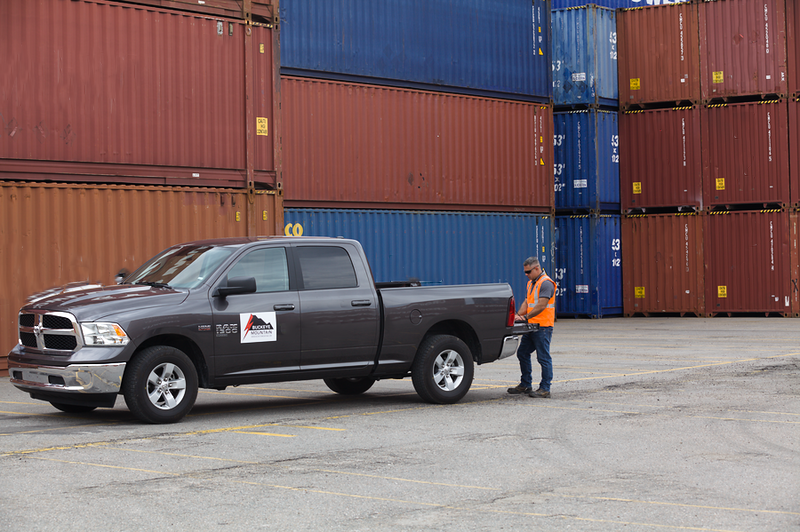
Outsourced equipment servicing not only helps you control hardware costs but also reduces the burden placed on in-house technicians.
It also allows your terminal to leverage the expertise of a service partner who can manage the entire equipment lifecycle for all of your assets—and do it better, more efficiently, and cheaper than your business could on its own.
When you choose Buckeye Mountain as your equipment service provider, you can expect the following:
Comprehensive Services
Buckeye Mountain is a value-added reseller across the rail, intermodal, and port industries. We offer competitive pricing and services tailored to your terminal’s unique needs.
When you contract with us as your equipment service provider, we work with you to develop a service plan that meets and exceeds your organization’s expectations. We go above and beyond our scope to deliver a turnkey solution that is flexible to your needs.
End-to-end Support
From product sourcing to lifecycle management, our service support covers equipment installation, training, maintenance, repair, and replacement—all to extend hardware lifespans, minimize operational disruptions, and maximize the value of your equipment investment.
Continuous Maintenance and Rapid Response
We quickly deploy a boots-on-the-ground presence when maintenance and repair services are required.
Our ongoing, on-site support provides continuous coverage for the full spectrum of equipment servicing needs, including rapid replacements and hardware upgrades to minimize downtime and ensure operational continuity.
Support Subscriptions for Managed Services
Expand your Buckeye Mountain service relationship by adding subscription options for 24/7 support. Our managed services can be configured to your facility’s unique needs, including remote and in-person support options.
We also offer coverage for a wide range of service needs, including network maintenance and equipment training.
Get the Most from Our Equipment Investment
Upgrading and replacing terminal hardware isn’t cheap. But if you don’t properly manage and maintain this new equipment, your long-term costs will soar—and the value of these assets will continue to decline until they reach the end of their lifecycle.
Buckeye Mountain can help you avoid this outcome. We provide a boots-on-the-ground presence to support your equipment across its lifespan, improving its longevity and availability while lowering costs and freeing up in-house resources.
Invest in your equipment by investing in Buckeye Mountain’s expertise.